Introduction
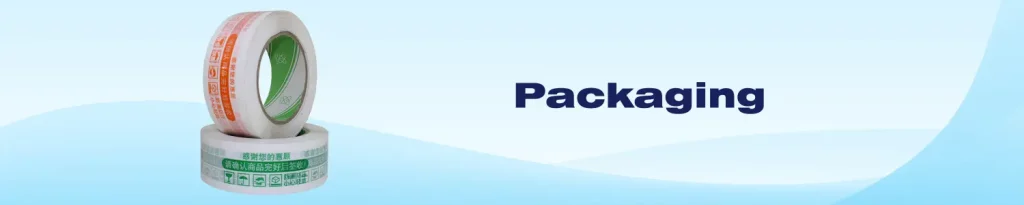
Industrial packaging tape plays a crucial role in the packaging industry, ensuring product safety, stability, and efficient transportation. Selecting high-quality, durable, and reliable adhesive tape is essential for businesses in various industries, including manufacturing, logistics, automotive, and electronics.
This guide will provide detailed insights into the key factors to consider when choosing industrial packaging tape, including material properties, adhesion strength, environmental compliance, industry applications, and performance testing methods.
1. Key Properties of Industrial Packaging Tape
When selecting industrial packaging tape, several properties should be evaluated to ensure it meets the specific requirements of your application.
1.1 Adhesion Strength
Adhesion strength determines how well the tape bonds to surfaces. Strong adhesion ensures that packages remain securely sealed, preventing product damage and contamination. Factors affecting adhesion strength include:
- Surface type: Rough, smooth, or porous surfaces require different adhesive formulations.
- Temperature resistance: High-temperature adhesives are necessary for heat-sensitive applications.
- Moisture resistance: Essential for tapes used in humid or wet environments.
1.2 Peel Strength
Peel strength measures the force required to remove the tape from a surface. Higher peel strength indicates better durability and resistance to external forces. Peel strength testing methods include:
- 90-degree peel test: Tape is peeled at a 90-degree angle under controlled conditions.
- 180-degree peel test: Similar to the 90-degree test but at a different angle, providing insights into long-term adhesion.
1.3 Tensile Strength and Elongation
Tensile strength refers to the maximum force a tape can withstand before breaking. High tensile strength is required for industrial applications where tape must endure stretching and tension.
Elongation measures how much the tape can stretch before breaking. Some applications, such as bundling heavy loads, require high elongation properties.
1.4 Temperature and Chemical Resistance
Industrial tapes must withstand extreme temperatures and exposure to chemicals. The following considerations are crucial:
- Heat-resistant tapes: Used in automotive and electronics industries.
- Cold-resistant tapes: Essential for freezer storage and cold chain logistics.
- Chemical-resistant tapes: Prevent degradation when exposed to solvents, oils, or acids.
2. Tape Types and Specifications
Industrial packaging tapes come in various types and specifications based on their intended applications.
2.1 Common Industrial Tape Types
Tape Type | Features | Application Examples |
---|---|---|
BOPP Tape | High adhesion, water-resistant | E-commerce, shipping, warehouse packaging |
Kraft Paper Tape | Eco-friendly, strong adhesion | Carton sealing, branding, and sustainable packaging |
Filament Tape | Reinforced with fiberglass, high tensile strength | Heavy-duty bundling and securing loads |
Double-sided Tape | Bonding strength on both sides | Mounting, automotive, and construction applications |
PVC Tape | Durable, moisture-resistant | Electrical insulation and industrial packaging |
2.2 Available Sizes and Thickness
Industrial tapes vary in width, thickness, and length. The most common sizes include:
Width (mm) | Thickness (microns) | Length (meters) |
---|---|---|
12, 24, 36, 48, 72 | 38 – 100 | 50 – 1000 |
Specialized tapes can be customized based on industry requirements.
3. Performance Testing Methods for Industrial Tape
Ensuring that packaging tape meets industrial standards requires rigorous testing. Some common testing methods include:
3.1 Adhesion and Peel Strength Testing
- ASTM D3330: Measures peel adhesion under controlled conditions.
- FINAT Test Method No. 1: Evaluates peel adhesion for pressure-sensitive tapes.
3.2 Tensile Strength and Elongation Testing
- ASTM D3759: Determines tensile strength and elongation limits.
- ISO 29862: Assesses the mechanical properties of adhesive tapes.
3.3 Environmental and Durability Testing
- UV exposure tests: Determines resistance to prolonged sunlight exposure.
- Aging tests: Evaluates tape performance over extended storage periods.
4. Environmental Compliance and Certifications
Sustainability and regulatory compliance are crucial considerations for packaging materials. Some key certifications include:
4.1 ISO 14001 – Environmental Management System
Ensures that packaging tape production meets global environmental standards.
4.2 ISO 9001 – Quality Management System
Guarantees consistency in manufacturing and product quality.
4.3 RoHS Compliance (Restriction of Hazardous Substances)
Ensures that tape materials do not contain hazardous substances like lead or mercury.
4.4 REACH Compliance
Verifies that tapes meet European chemical safety regulations.
4.5 FDA Compliance (For Food-Grade Tapes)
Ensures that tapes used in food packaging are safe and non-toxic.
5. Industry Applications of Industrial Packaging Tape
Packaging tapes are widely used across multiple industries. Below are some common applications:
5.1 Automotive Industry
- Heat-resistant and chemical-resistant tapes for wire harnessing and component assembly.
5.2 Electronics Industry
- PVC and PET tapes for circuit board insulation and component protection.
5.3 Logistics and E-Commerce
- BOPP and reinforced tapes for secure carton sealing and package reinforcement.
5.4 Food and Beverage Industry
- FDA-compliant tapes for safe food packaging and transport.
5.5 Construction Industry
- High-bond double-sided tapes for mounting, sealing, and structural bonding.
6. How to Choose the Right Packaging Tape
Step-by-Step Selection Guide
- Determine Application Requirements: Identify whether the tape is for general packaging, industrial sealing, or specialized applications.
- Select the Right Material: Choose based on adhesion strength, temperature resistance, and durability.
- Check Size and Thickness: Ensure the tape dimensions match your packaging needs.
- Evaluate Performance Standards: Verify compliance with ASTM, ISO, or RoHS certifications.
- Consider Cost and Supplier Reliability: Partner with reputable manufacturers to ensure quality consistency.
Conclusion
Choosing the right industrial packaging tape involves assessing adhesion strength, material durability, environmental compliance, and industry applications. By understanding these factors, businesses can improve packaging efficiency, enhance product protection, and meet sustainability goals.
For customized packaging solutions, reach out to our team or explore our range of industrial adhesive tapes.

Products
Rich variety of adhesive tape